23 Seacraft rebuild, scepter to open fisherman
Page 1 of 1
23 Seacraft rebuild, scepter to open fisherman
Staring this thread for a customer.
Scepter hull, with good stringers. Needs new transom, raise stringers by at least 2".
I dont recall if you want a plywood or foam core transom, but the proceedure is the same either way. After you have the hull braced up well, you cut the cap and pull it off so you have access to the entire transom. Cut back stringers by about 12".
If you plan to run your new sole/deck all the way back to the transom, then you will need to do the transom first, before raising the stringers. This way you can patch back in the stringer to the transom before raising the stringer level
Second project is to raise stringers. Its nice that you still have the tops on the stringers, you can just epoxy down some high density core, then cover them with one layer of glass (overlapping back down the sides of the stringers. 4" overlap is plenty in this case, your only making sure the deck has something good to bond to. If you glued the deck right down to the foam, then your bond would be to the foam instead of to glass that is attached to the stringers - hope that makes sense. I have a lot of this 20 lb foam in 2" thickness that will be perfect for this application
http://www.gulfstreamcomposites.com/product-p/lhm_foamplank.htm

After stringers are finished, you build your transverse framing. To add stiffness to the hull, these frames do not necessarily have to be all the way to the stringer top level in , but I would extend them all the way up, it makes for more bonding area and support for the new sole/deck. These can be made from foam core or from honeycomb.
Do you plan to re-use the liner? I think I remember from our conversation that you do not, but I cant be sure. If you plan to reuse the liner, then you need the same foam spacer on the "lip" of the liner so the new deck will be the same level.
Building the new cap/gunnels is the last thing to do. Since you are starting with a cut back scepter cap, you can make it whatever shape you want. For core material, you would normally use a light foam, but its not going to be rigid enough to shape. This is going to be a little tricky, you need to build the coaming section (vertical section of cap) in a way that you do not have to glass the underside while upside down. Here is one solution: Using a foam rigid enough to hold its shape, dry fit the core, use screws to hold it. (by this time, you will also have frames/stiffeners on the hullside to support the new cap). Trim the shape you want. Now you will attach the coaming core, use screws to hold it while you epoxy glue the flat section of cap to the coaming. Now the tricky part, you flip this over and glass the underside of the cap, joining the flat section to the coaming. Then flip back over, run a router around the coaming joint and glass the topside to the coaming and the lip of the old cap.
more to come......

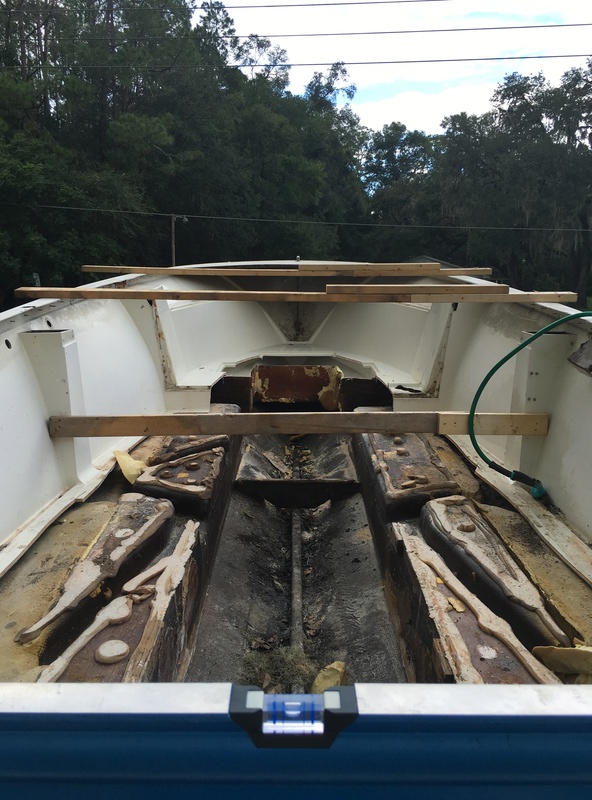
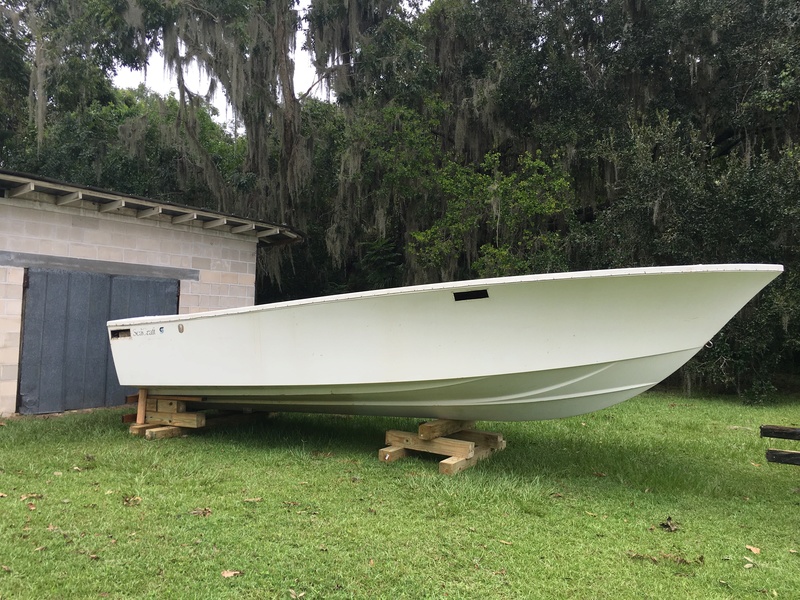
this is similar to what the final desired product will be
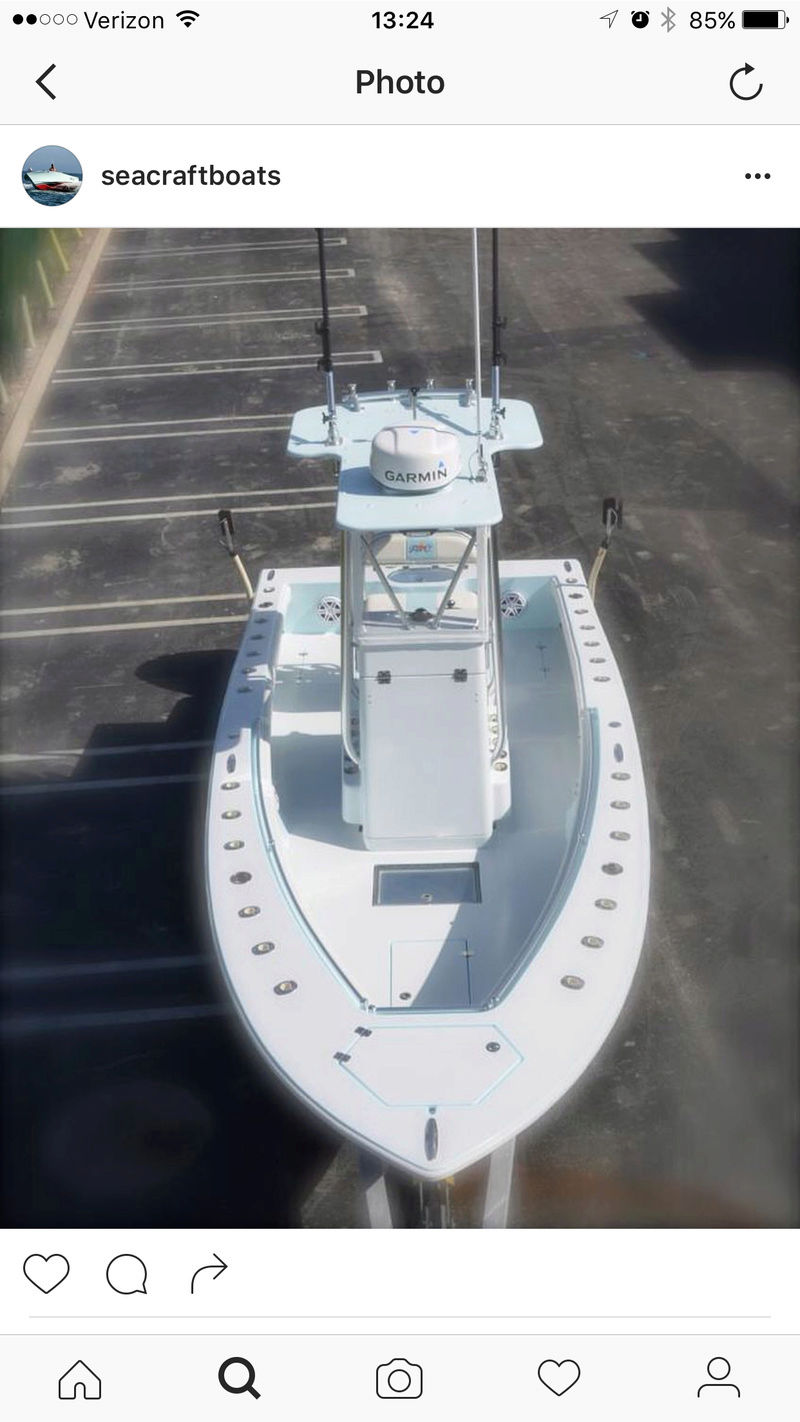
Scepter hull, with good stringers. Needs new transom, raise stringers by at least 2".
My plan with this boat Is to turn it into an open fisherman with no step in the deck. I plan on the cap tapering from 24" wide in the bow to fit the original gunnel in the rear. Keeping foot room in mind while fetching the anchor or fighting a fish in rough water. I plan on removing all of the wood under the gunnels in the bow and the gunnels I left in place in the stern. So I will need core material for the gunnel all the way around. I would like for the drop down on the gunnel to be core material as well. The only hand rail will be directly the behind the anchor locker in the bow. I would like to raise the stringers two inches and use the honeycomb for the core in the deck. The transom will definitely need to be replaced. The fuel tank will be 150 gallons which makes it exactly 8 foot long, so I'll need core for under the tank. Core for the live well/ fish box and dry storage/ fish box. I'll send you some better pictures later this week along with some dimensions of the gunnels and dry storage/fish box/live well. I plan on adding 4 bulkheads to the boat for strength and rigidity.
I dont recall if you want a plywood or foam core transom, but the proceedure is the same either way. After you have the hull braced up well, you cut the cap and pull it off so you have access to the entire transom. Cut back stringers by about 12".
If you plan to run your new sole/deck all the way back to the transom, then you will need to do the transom first, before raising the stringers. This way you can patch back in the stringer to the transom before raising the stringer level
Second project is to raise stringers. Its nice that you still have the tops on the stringers, you can just epoxy down some high density core, then cover them with one layer of glass (overlapping back down the sides of the stringers. 4" overlap is plenty in this case, your only making sure the deck has something good to bond to. If you glued the deck right down to the foam, then your bond would be to the foam instead of to glass that is attached to the stringers - hope that makes sense. I have a lot of this 20 lb foam in 2" thickness that will be perfect for this application
http://www.gulfstreamcomposites.com/product-p/lhm_foamplank.htm

After stringers are finished, you build your transverse framing. To add stiffness to the hull, these frames do not necessarily have to be all the way to the stringer top level in , but I would extend them all the way up, it makes for more bonding area and support for the new sole/deck. These can be made from foam core or from honeycomb.
Do you plan to re-use the liner? I think I remember from our conversation that you do not, but I cant be sure. If you plan to reuse the liner, then you need the same foam spacer on the "lip" of the liner so the new deck will be the same level.
Building the new cap/gunnels is the last thing to do. Since you are starting with a cut back scepter cap, you can make it whatever shape you want. For core material, you would normally use a light foam, but its not going to be rigid enough to shape. This is going to be a little tricky, you need to build the coaming section (vertical section of cap) in a way that you do not have to glass the underside while upside down. Here is one solution: Using a foam rigid enough to hold its shape, dry fit the core, use screws to hold it. (by this time, you will also have frames/stiffeners on the hullside to support the new cap). Trim the shape you want. Now you will attach the coaming core, use screws to hold it while you epoxy glue the flat section of cap to the coaming. Now the tricky part, you flip this over and glass the underside of the cap, joining the flat section to the coaming. Then flip back over, run a router around the coaming joint and glass the topside to the coaming and the lip of the old cap.
more to come......

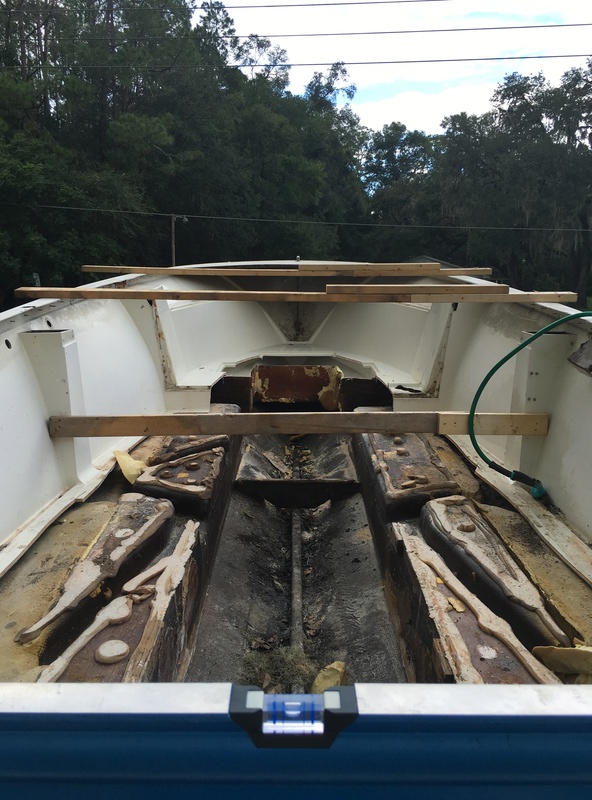
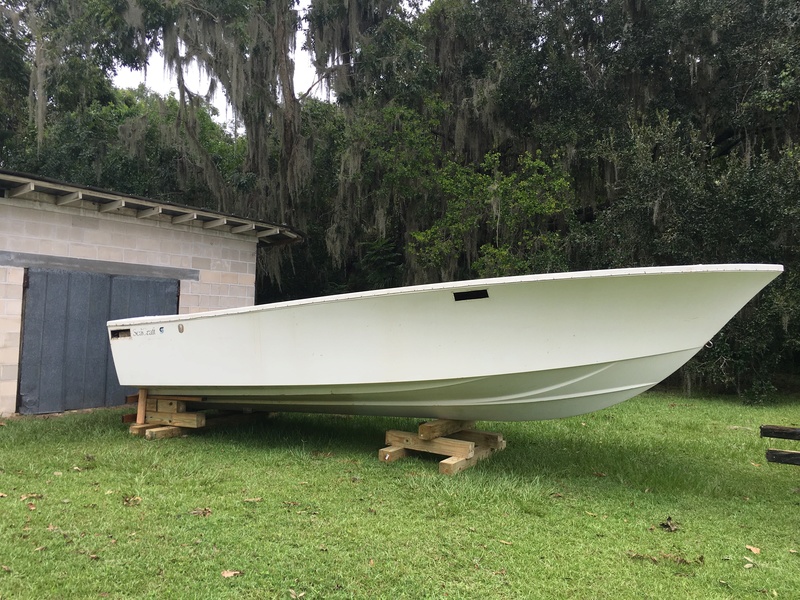
this is similar to what the final desired product will be
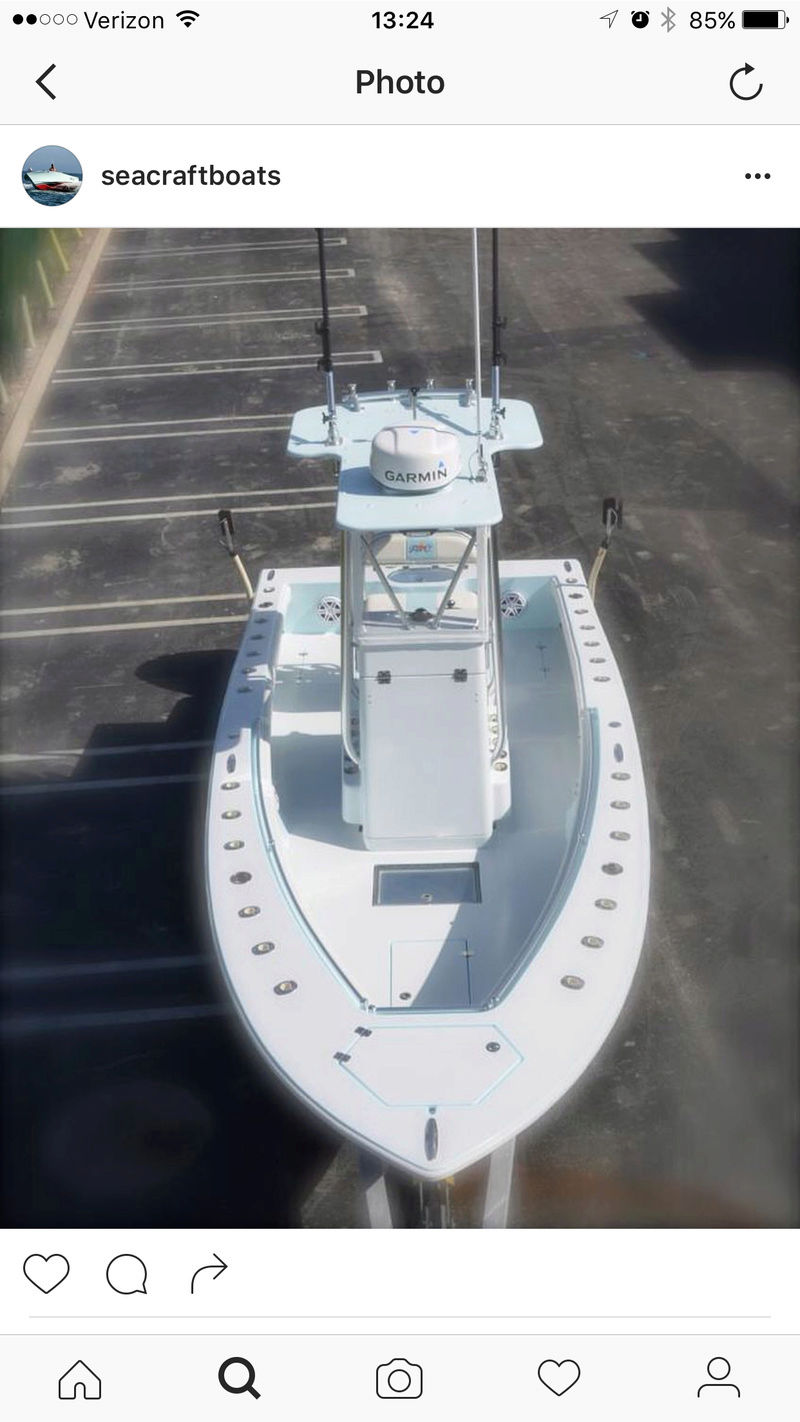
Re: 23 Seacraft rebuild, scepter to open fisherman
Thanks for the sketch, looks like a good set up. The rear cap is relatively narrow, not much room when you take into account the angle of the transom.
It does not necessarily need to be any wider if you dont want, but there isnt going to be much room under there for rigging.
I will break the materials down by steps:
Transom:
core: I have a couple pieces of 1.5" transom foam left from my boat project. Its 4'x4', so you would need two pieces. The other alternative is 2 layers of
the coosa is more expensive, but either one is a good material. http://www.gulfstreamcomposites.com/category-s/136.htm
Resin: You will need about 5 gallons of epoxy to glue in and glass in the new transom core. 6 gallon epoxy kit here
Fillers: 2 lbs wood flour and 8 oz silica. This is mixed together to make a filler for glue and fillets. link to fillers here
Glass: Tabbing: 12 yards of 12 oz biax tape. Inside skin: You will need at least 3 layers of 1708 to build up to a thickness of 3/16". The inside skin overlaps the sides and
bottom (covering the tabbing). 3 layers is going to be 10 yards of 1708 50" wide biaxial fiberglass here
Raising stringers:
Core: I have these 2" thick planks that are perfect for this application, they are 8" wide, 2" thick, and 48" long. You will have to measure out the stringers to see how many you need.
the best part of these is that you do not need much glass over top.
Fillers: Another 2 lb WF and 8 oz silica to make glue to bed the foam to the tops of the stringers
glass: one layer of 1708 overtop the foam, overlapping down the stringer sides by at least 4". Will need measurements of the stringer tops so we can determine how much 1708 this takes
Resin: Depends on the amount of 1708, but your probably going to use about 3 gallons for the whole stringer job
Transverse stiffeners (below the sole):
These frames will really help stiffen up the hull. For core, I would use a foam core or marine plywood. I understand if you want to avoid plywood. It OK to use honeycomb too and depending on
your waste cut offs you may have enough from the sole to do a couple frames. Problem is you have to make the sole first in order to use waster from it for the frames
Core: 3/4" - need to know dimensions to give accurate estiamate, but I cant imgine needing less than 3 sheets for these
fillers: a little more fillers to make fillets to glass frames to stringers and hull
Resin: Rough guess, 3 gallons
Glass: 1708 to cover both sides of core - rough guess 15 yards. Two layers of 12 oz biax tape to glass frame parts to stringers/hull - rough guess 75 yards (there is a lot of tabbing joints when
you measure all around the frame parts.
Sole:
You have a couple options here. I like honeycomb for a sole, either the pre-glassed panels or make your own. The pre-glassed panels make things a little easier, but you have to
plan for the splices. If you lay out your own sole, using just the core, then glassing both sides yourself, it eliminates the splices. Really it comes down to how much space you have, laying
out a sole takes up a lot of space. I remember my SC23 took 4 4x8 panels to do the sole, but you need to measure that out. Optional: if you make your own sole, you can use vinylester
resin to glass the skins. Vinylester is great for wetting out the 1708, and its very stiff - you will then tab it to the hull with epoxy. Vinyester/polyester is fine for making parts, but attaching
parts (secondary bonding) there is no comparison to epoxy.
Core: 4 sheets of 25mm (1") core
fillers: Another 2 lb WF and 8 oz silica to make glue to bed the sole to tops of stringersand frames
Resin: if you make your own from raw core, 5 gallons to laminate skins, another 1.5 epoxy to tab sole to sides of hull
Glass: making your own - 1708 each side, which makes about 22 yards. 12 oz biax tape for tabbing sole to sides: 30 yards.
optional: if you use the pre-glassed panels, you may want to cover the top sides with a layer of extra glass (10 oz woven). The panels are plenty strong, but the skins are thin.
I would do this, its not much more work and only adds roughly 16 lbs to the boat (10oz over 32 square feet + the epoxy to wet it out get you to 16 lbs)
Transverse stiffeners above the sole:
You have a lot of choices here. You can core the entire side of the hull and eliminate the need for any frames, this is a lot of work and uses quite a bit more materials, but it
gives a very clean look. You can also make frames with the high density foam planks (same stuff used to raise the stringer level). I also have fiberglass forms that you can glass
to the sides to make hollow frames, which are nice for running gas fill/vent lines. Not much sense in speculating one material uses until we know what direction you want to go.
New Cap:
You are creating a new deck/gunnel using the existing cap from a scepter. There are more than a few options on how to do this and they all have there own challenges.
Option 1: Use marine plywood, this is the easiest and least expensive, but its wood and if you dont want wood I understand
Option 2: Use a high density foam like the 3/4" transom foam. This is heavy, but its stiff and easy to form (like wood), it also means you will not need to worry about any inserts around
hardware. High density foam also means you need less glass than a light weight core.
Option 3: Use a light weight core/foam. More difficult to form (isnt stiff), need more glass on the topsides, and you have to put in higher density inserts around hardware.
Once we decide on which way you want to go on this, I can make a material list.
Something else to consider: If you use the 3/4" high density foam for the gunnels/deck, you can use off cuts for the transverse frames or the other way around. Its always a
good idea to use materials that can be used in multiple applications, makes for less waste and no down time if you run out of a particular material.
Lets discuss which materials you want to use for a core, and then I can make a more detailed list. Its a good idea to get the core all at once to avoid multiple trips or freight.
The epoxy/glass can all go by UPS and we cover shipping (next day in FL) on larger order, so running out of epoxy/glass/fillers/etc is not such a big deal.
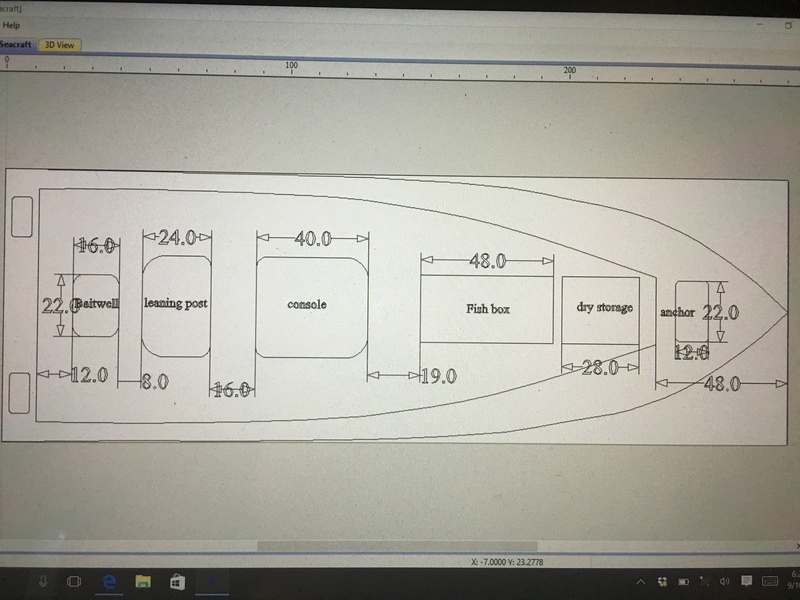
It does not necessarily need to be any wider if you dont want, but there isnt going to be much room under there for rigging.
I will break the materials down by steps:
Transom:
core: I have a couple pieces of 1.5" transom foam left from my boat project. Its 4'x4', so you would need two pieces. The other alternative is 2 layers of
the coosa is more expensive, but either one is a good material. http://www.gulfstreamcomposites.com/category-s/136.htm
Resin: You will need about 5 gallons of epoxy to glue in and glass in the new transom core. 6 gallon epoxy kit here
Fillers: 2 lbs wood flour and 8 oz silica. This is mixed together to make a filler for glue and fillets. link to fillers here
Glass: Tabbing: 12 yards of 12 oz biax tape. Inside skin: You will need at least 3 layers of 1708 to build up to a thickness of 3/16". The inside skin overlaps the sides and
bottom (covering the tabbing). 3 layers is going to be 10 yards of 1708 50" wide biaxial fiberglass here
Raising stringers:
Core: I have these 2" thick planks that are perfect for this application, they are 8" wide, 2" thick, and 48" long. You will have to measure out the stringers to see how many you need.
the best part of these is that you do not need much glass over top.
Fillers: Another 2 lb WF and 8 oz silica to make glue to bed the foam to the tops of the stringers
glass: one layer of 1708 overtop the foam, overlapping down the stringer sides by at least 4". Will need measurements of the stringer tops so we can determine how much 1708 this takes
Resin: Depends on the amount of 1708, but your probably going to use about 3 gallons for the whole stringer job
Transverse stiffeners (below the sole):
These frames will really help stiffen up the hull. For core, I would use a foam core or marine plywood. I understand if you want to avoid plywood. It OK to use honeycomb too and depending on
your waste cut offs you may have enough from the sole to do a couple frames. Problem is you have to make the sole first in order to use waster from it for the frames
Core: 3/4" - need to know dimensions to give accurate estiamate, but I cant imgine needing less than 3 sheets for these
fillers: a little more fillers to make fillets to glass frames to stringers and hull
Resin: Rough guess, 3 gallons
Glass: 1708 to cover both sides of core - rough guess 15 yards. Two layers of 12 oz biax tape to glass frame parts to stringers/hull - rough guess 75 yards (there is a lot of tabbing joints when
you measure all around the frame parts.
Sole:
You have a couple options here. I like honeycomb for a sole, either the pre-glassed panels or make your own. The pre-glassed panels make things a little easier, but you have to
plan for the splices. If you lay out your own sole, using just the core, then glassing both sides yourself, it eliminates the splices. Really it comes down to how much space you have, laying
out a sole takes up a lot of space. I remember my SC23 took 4 4x8 panels to do the sole, but you need to measure that out. Optional: if you make your own sole, you can use vinylester
resin to glass the skins. Vinylester is great for wetting out the 1708, and its very stiff - you will then tab it to the hull with epoxy. Vinyester/polyester is fine for making parts, but attaching
parts (secondary bonding) there is no comparison to epoxy.
Core: 4 sheets of 25mm (1") core
fillers: Another 2 lb WF and 8 oz silica to make glue to bed the sole to tops of stringersand frames
Resin: if you make your own from raw core, 5 gallons to laminate skins, another 1.5 epoxy to tab sole to sides of hull
Glass: making your own - 1708 each side, which makes about 22 yards. 12 oz biax tape for tabbing sole to sides: 30 yards.
optional: if you use the pre-glassed panels, you may want to cover the top sides with a layer of extra glass (10 oz woven). The panels are plenty strong, but the skins are thin.
I would do this, its not much more work and only adds roughly 16 lbs to the boat (10oz over 32 square feet + the epoxy to wet it out get you to 16 lbs)
Transverse stiffeners above the sole:
You have a lot of choices here. You can core the entire side of the hull and eliminate the need for any frames, this is a lot of work and uses quite a bit more materials, but it
gives a very clean look. You can also make frames with the high density foam planks (same stuff used to raise the stringer level). I also have fiberglass forms that you can glass
to the sides to make hollow frames, which are nice for running gas fill/vent lines. Not much sense in speculating one material uses until we know what direction you want to go.
New Cap:
You are creating a new deck/gunnel using the existing cap from a scepter. There are more than a few options on how to do this and they all have there own challenges.
Option 1: Use marine plywood, this is the easiest and least expensive, but its wood and if you dont want wood I understand
Option 2: Use a high density foam like the 3/4" transom foam. This is heavy, but its stiff and easy to form (like wood), it also means you will not need to worry about any inserts around
hardware. High density foam also means you need less glass than a light weight core.
Option 3: Use a light weight core/foam. More difficult to form (isnt stiff), need more glass on the topsides, and you have to put in higher density inserts around hardware.
Once we decide on which way you want to go on this, I can make a material list.
Something else to consider: If you use the 3/4" high density foam for the gunnels/deck, you can use off cuts for the transverse frames or the other way around. Its always a
good idea to use materials that can be used in multiple applications, makes for less waste and no down time if you run out of a particular material.
Lets discuss which materials you want to use for a core, and then I can make a more detailed list. Its a good idea to get the core all at once to avoid multiple trips or freight.
The epoxy/glass can all go by UPS and we cover shipping (next day in FL) on larger order, so running out of epoxy/glass/fillers/etc is not such a big deal.
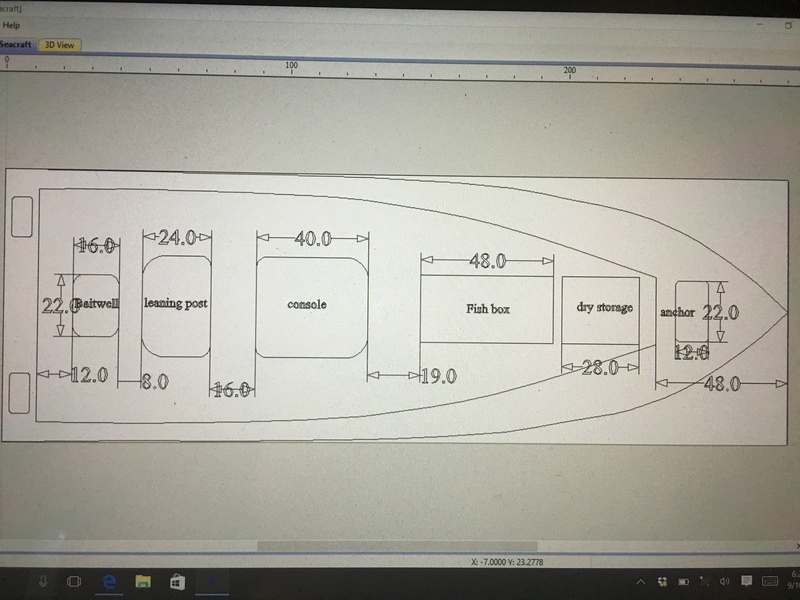

» 23 Seacraft rebuild, Charleston SC
» local Seacraft 23 rebuild
» Another Seacraft Project
» Mako 17 rebuild
» Cobia Rebuild
» local Seacraft 23 rebuild
» Another Seacraft Project
» Mako 17 rebuild
» Cobia Rebuild
Page 1 of 1
Permissions in this forum:
You cannot reply to topics in this forum